- Development Engineer Interview
ADAS Chassis
Q. What made you develop the ADAS chassis?
Originally, we have offered our EV platform chassis to various clients with the Tommykaira ZZ* (*hereinafter referred to as the ZZ) as a base vehicle in our EV platform business. Those clients have used them as show cars and test vehicles. But now, there has been much progress in the development of autonomous driving technology. Under such circumstances, the ZZ will no longer be able to meet the need of clients because the ZZ doesn’t have an electric steering system, its brake doesn’t have a booster, and the ZZ is a manual transmission car. Then, we thought by making those functions controllable electrically, we can make a platform that can be used for autonomous driving. So, we developed the ADAS chassis to expand our EV platform business to clients who are engaging in autonomous development.
Q. What are the features of the ADAS chassis?
One of its outstanding features is its stick proportional radio control system. You can control the vehicle just like you drive a radio-controlled car. Also, you can steer the vehicle electronically and stop the vehicle remotely without putting on the brake pedal. Since the ADAS chassis has the same motor as the one on the ZZ, the vehicle can run quite fast if you want. And its braking control works stronger and faster than a human pitting on the brake pedal. That means you can enjoy the same level of performance as driving behind the wheel. With this EV, clients can make various assessments and verifications.
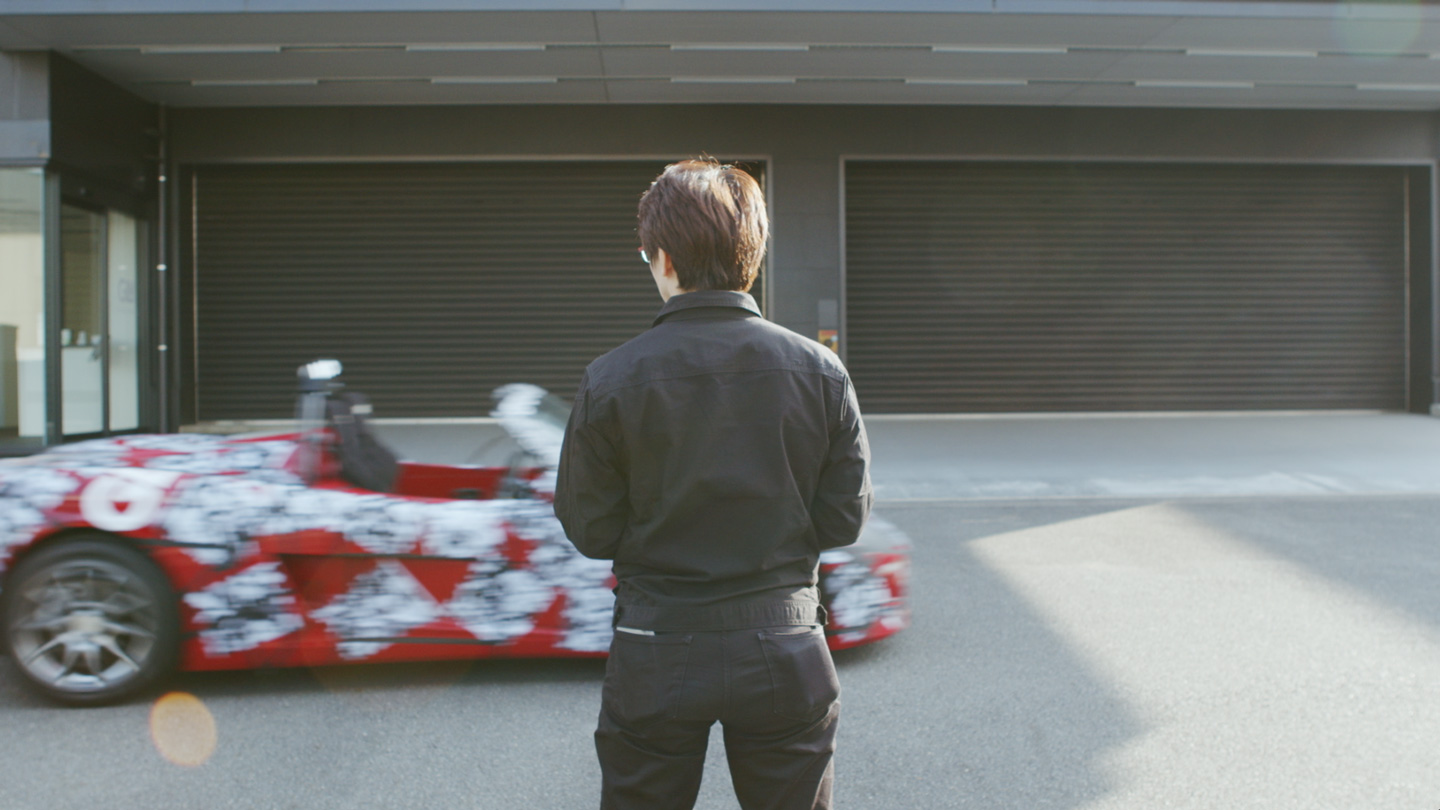
Q. What R&D can be done with the ADAS chassis?
One of the possible cases would be a test with the ADAS chassis. For instance, a supplier who develops autonomous driving software can equip and test their software and their client’s autonomous driving components on the ADAS chassis, a real-size car. Of course, it is possible to install and test their products on a car available in the market. But it would be difficult. First, the car needs to be altered for their test considerably. Second, the manufacturers of those cars don’t disclose all the information on those cars. So, they have to conduct a test without all the information on the car. But if they use the ADAS chassis to test their products, they’ll have access to all the information including the control system, the power performance, and all the relation of numerical values because we can share all the information on the vehicle for accurate verifications and testing.
Q. What development was made for the ADAS chassis?
The configuration of the ZZ, the base vehicle is quite simple. So, it was difficult to adapt the control system network when installing a cutting-edge brake system and electric steering system. Putting together the simple base vehicle structure and new parts to build a car capable of running was a technically difficult part of the development. When the car was completed, all the new parts and the simple structure fit and work well together. Also, since we developed the whole computer dedicated to the ADAS chassis, which enables integrated control, the vehicle is very coordinated and highly controllable.
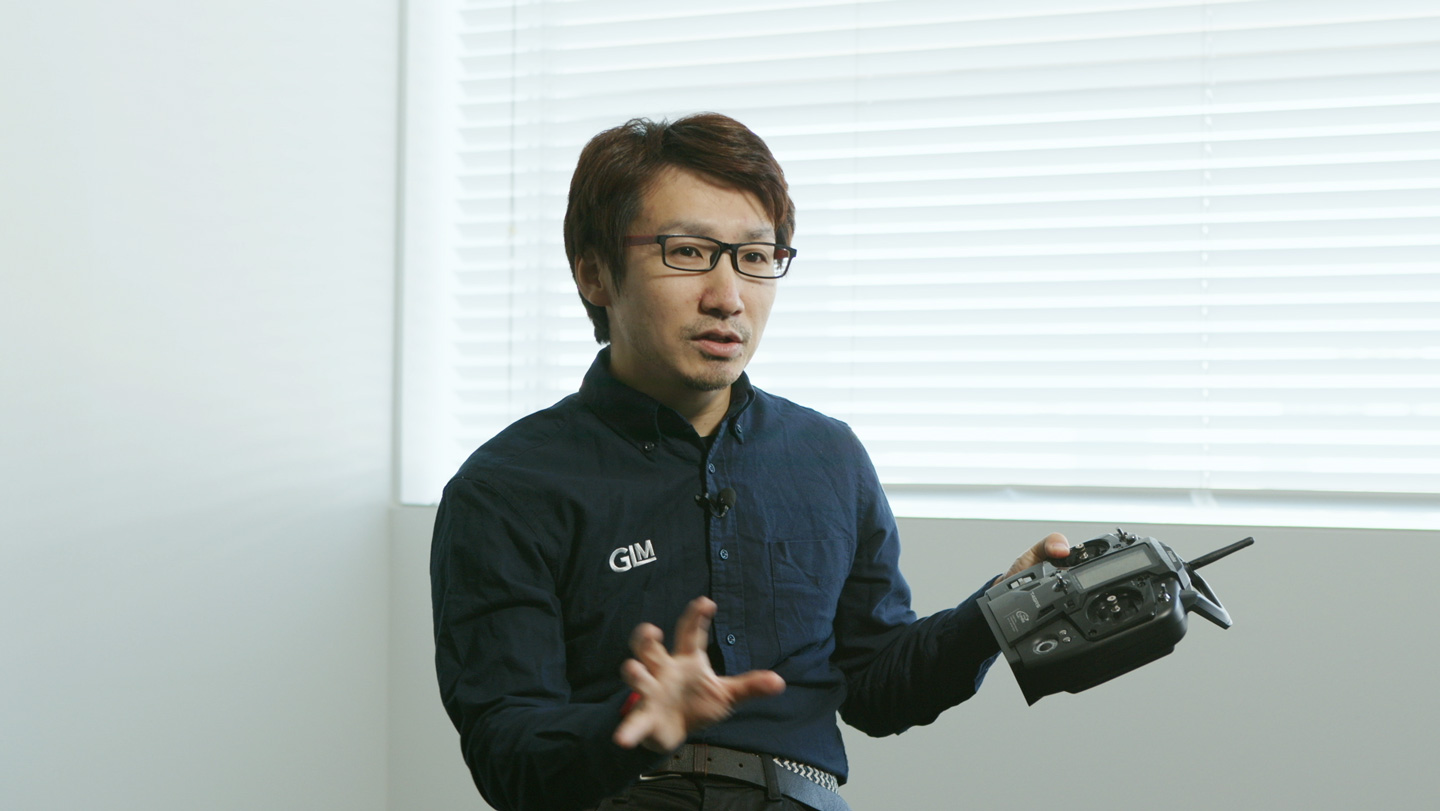
Q. Please tell me the difficulties in developing the ADAS chassis?
The proportional radio-control system has a transmitter and a receiver with a small antenna. The ECU converts signals received by the receiver to a certain value. But there is not so much information on the signal coming from the receiver, so, we needed to analyze it. So, making it radio-controlled was one of the most difficult parts. Since the ADAS chassis moves in accordance with outside signals coming from the proportional RC system, with the development of ECUs, the car can be responsive to different outside signals. So, I think it can be changed according to the needs of clients.
Q. How did you feel when you controlled the ADAS chassis remotely for the first time?
At first, it was quite scary. The ADAS chassis moves depending on the voltage of its accelerator. And it was very difficult to know how the ADAS chassis accelerates responding to the stick control. I learned how to move it soon, but I spent much time fine-tuning it in tune with human senses. The power is set at as low as 30% by the default setting. Because if it’s set at about 60%, just by pulling the stick a little bit, the vehicle accelerates very fast. So, for safety, the power is always set at low. But if you can drive it in a spacious place like an airport, you can drive it at a full speed and enjoy the real performance of the vehicle. It is so much fun.
Q. Is it difficult to control the ADAS chassis?
It would be difficult if you are not used to driving RC cars simply because, like RC cars, when the car comes towards you, the steering of right or left is reversed. So, when the car backs toward you, you’ll be especially confused about which direction the car is going. So, controlling it is just as tricky as controlling RC cars. And of course, I can never crash the car. So, at first, I was quite nervous when driving, but now I am used to it a little.
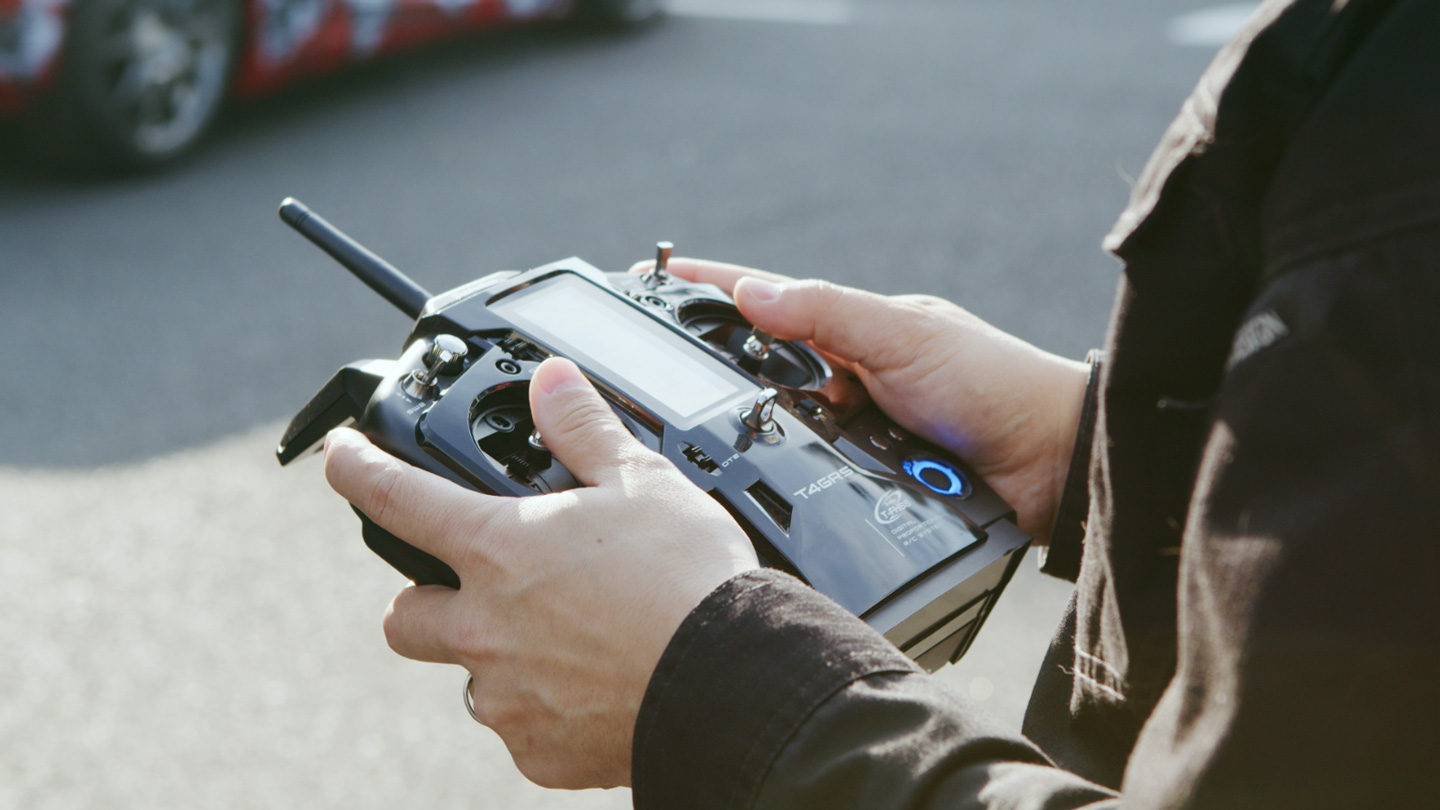
Q. For what kind of company’s R&D can the ADAS chassis be helpful?
The ADAS chassis is suitable for those who are engaging in various research such as an algorithm for autonomous driving and the development of software simulators. Although Various algorithms can be verified on computer simulations, the verifications and testing with an actual car can be challenging for them. So, we will be providing the ADAS chassis, a real car for these clients. In addition to that, manufacturers who develop sensors like LiDAR and cameras can verify and test their products using the ADAS chassis because these manufacturers face difficulties by the lack of access to the information they need. After all, much information or data can be available only by testing with a real car. So, we want to recommend these manufacturers test their products with the ADAS chassis so that they can give feedback on the results. I think there are many business opportunities where they can go to a major manufacturer and appeal their products with the test results gained with the ADAS chassis.
Profile
Tatsuya Yamakawa
Born in 1983, from Nagano. Involved in research and development of next-generation refrigeration vehicles and air conditioning technology at Topre Co., Ltd., applied for 3 patents. After that, Engaged in the development of air conditioning systems for plug-in hybrid vehicles at Subaru Corporation, before joining GLM. Experienced in the development of air conditioning systems for EV supercars and electrical and electronic systems. As a project manager for a commissioned project using an EV platform Participated in the development of a test vehicle equipped with mechanical and electrical integrated e-axles for the front and rear of Univance Co., Ltd. Established Route7 Automotive Inc. in 2019, consistently in charge of ECU development in EV platforms for ADAS and vehicle control As chief engineer of EE system development.